Authored by: Mr. Aveen Padmaprabha, Head of Industrial High quality Options, Carl Zeiss India (Bangalore) Pvt. Ltd.
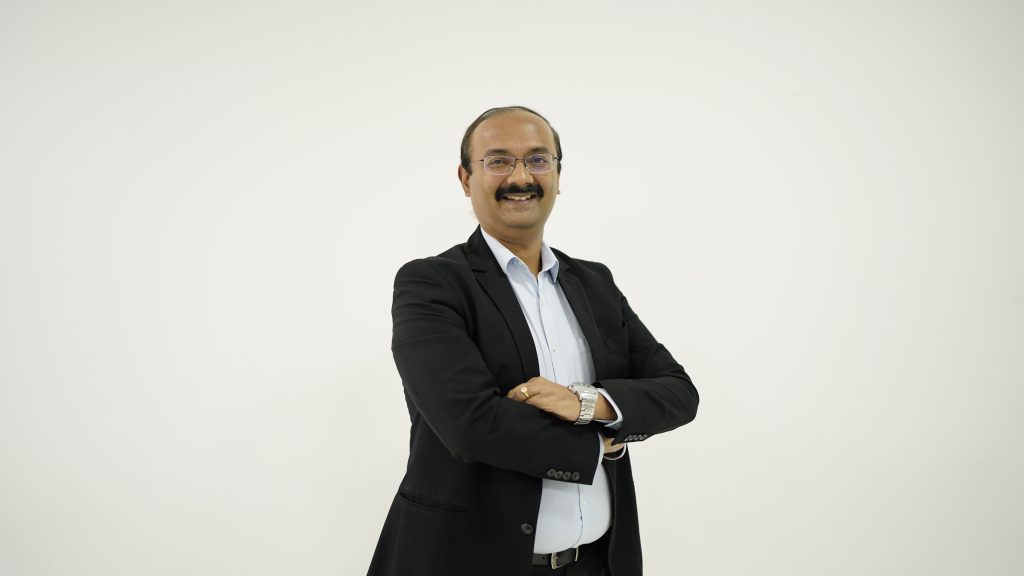
The aerospace business in India is among the fastest-growing sectors with an more and more robust home manufacturing base. To achieve additional aggressive benefit, the implementation of latest applied sciences corresponding to additive manufacturing has been gaining significance within the current previous. Whereas this technique results in value discount of constructing low-volume elements, in addition to permits the business to problem the boundaries of effectivity by extraordinarily correct and sophisticated design executions, the standard challenges confronted by these new manufacturing processes must also be completely addressed. Excessive-precision metrology options aren’t solely a possibility to optimize the manufacturing course of but in addition provide helpful perception into materials sciences and make sure the high quality of the output.
Additive Manufacturing as an Alternative in Aerospace
Air journey, a most popular mode of transportation, depends on plane elements assembly stringent high quality requirements. For example, earlier than a provider commences manufacturing, as much as 1500 inspection options of a turbine blade have to be verified, adhering to tight tolerance ranges at each manufacturing step. Past this problem, one other is the very important upkeep and restore operations (MRO) which regularly includes changing high-complexity, quality-intensive low-volume or single elements. Conventional manufacturing processes for MROs show each time and cost-intensive, unable to satisfy the demanded complexity and accuracy effectively. Consequently, additive manufacturing, particularly 3D printing, is more and more built-in into the aerospace manufacturing chain in India, positioning the business as a pioneer in additive manufacturing innovation. Nonetheless, the adoption of this know-how brings its personal challenges, which our expertise suggests might be successfully addressed by high-quality metrology options.
Hitting the Brake: The Course of and Challenges of Additive Manufacturing
Powder is the constructing block of additively manufactured elements. The particles are small, usually starting from a number of micrometers to tens of microns in diameter. Their measurement distribution and form affect unfold capacity and therefore doable defects would possibly happen throughout the course of. The defect density is amongst different elements and in addition an element for the recycling and ageing of the powder. A uniformly distributed powder mattress is the important foundation for a steady and dependable additive manufacturing course of. Improper powder high quality, powder rheology and the method parameters would possibly trigger voids to type within the ultimate construction. The additive manufacturing course of, in contrast to conventional manufacturing strategies, requires powders to be melted layer by layer throughout the construct. Soften temperatures and course of parameters enormously have an effect on the crystallography and, as a consequence, half properties. After printing, the half remains to be connected to the construct plate. It’s then heat-treated for stress aid and faraway from the construct plate with a band noticed or wire EDM. Some elements are then warmth handled once more for microstructure adjustments. These processes presumably affect the traits and accuracy of the half, impacting the standard and security. Publish which, Dimensional accuracy and floor end are essential to make sure correct meeting and constant matching throughout a number of elements. Though additive manufacturing is an immense alternative because it permits an unprecedented management over materials microstructures. Analyzing and understanding these constructions is vital for an environment friendly and optimized course of that ensures the demanded high quality and security.
Precision in any respect Altitudes: Overcoming the Challenges
Using cutting-edge measurement and inspection tools is essential for assembly aerospace elements’ subtle necessities. Our metrology options assist and might be carried out all through the manufacturing course of, enabling quick corrective actions, making certain high-quality output, and selling sustainable resourcing. We make use of Mild or Electron Microscopes and CT for steady powder characterization, figuring out sources of high quality points within the powder mattress throughout or after printing. Faulty elements might be detected and glued throughout the construct, avoiding downstream prices and rising yield. Optical 3D-scanners, Coordinate Measuring Machines, and high-resolution CT validate accuracy, examine completed elements, and analyze inner constructions, contributing to defining optimum settings for future processes. The great information evaluation throughout the method chain, facilitated by metrology gadgets outfitted with IoT and PiWeb software program by ZEISS, ensures correlation and helps an environment friendly and optimized course of. Investing in high-quality metrology and analysis tools is indispensable for making certain security and high quality within the aerospace business, significantly as ‘Make in India’ propels the sector’s development, with additive manufacturing taking part in an important position in materials science and course of optimization.
ZEISS, as a key world supplier, performs a pivotal position with its Blue Line course of, contributing to the business’s success by exact metrology and high quality options. Furthermore, the corporate’s dedication to excellence extends past mere provision, because it actively engages in collaborative ventures. The corporate’s globally distinctive software lab not solely facilitates joint buyer initiatives and scientific research but in addition serves as a dynamic hub for hands-on demonstrations. This collaborative method fosters a wealthy atmosphere for studying and data distribution, making certain that the aerospace business advantages not solely from cutting-edge know-how but in addition from shared insights and collective experience.
For my part, the aerospace business in India stands on the forefront of innovation and technological developments, embracing additive manufacturing as a vital factor in its manufacturing chain. By leveraging cutting-edge measurement and inspection tools all through your complete manufacturing course of, the business can obtain quick corrective actions, improve yield, and streamline useful resource utilization. With continued investments in high-quality metrology and analysis tools, the aerospace sector can guarantee the security and high quality of its intricate and sophisticated elements, additional solidifying its place as a frontrunner in technological innovation.